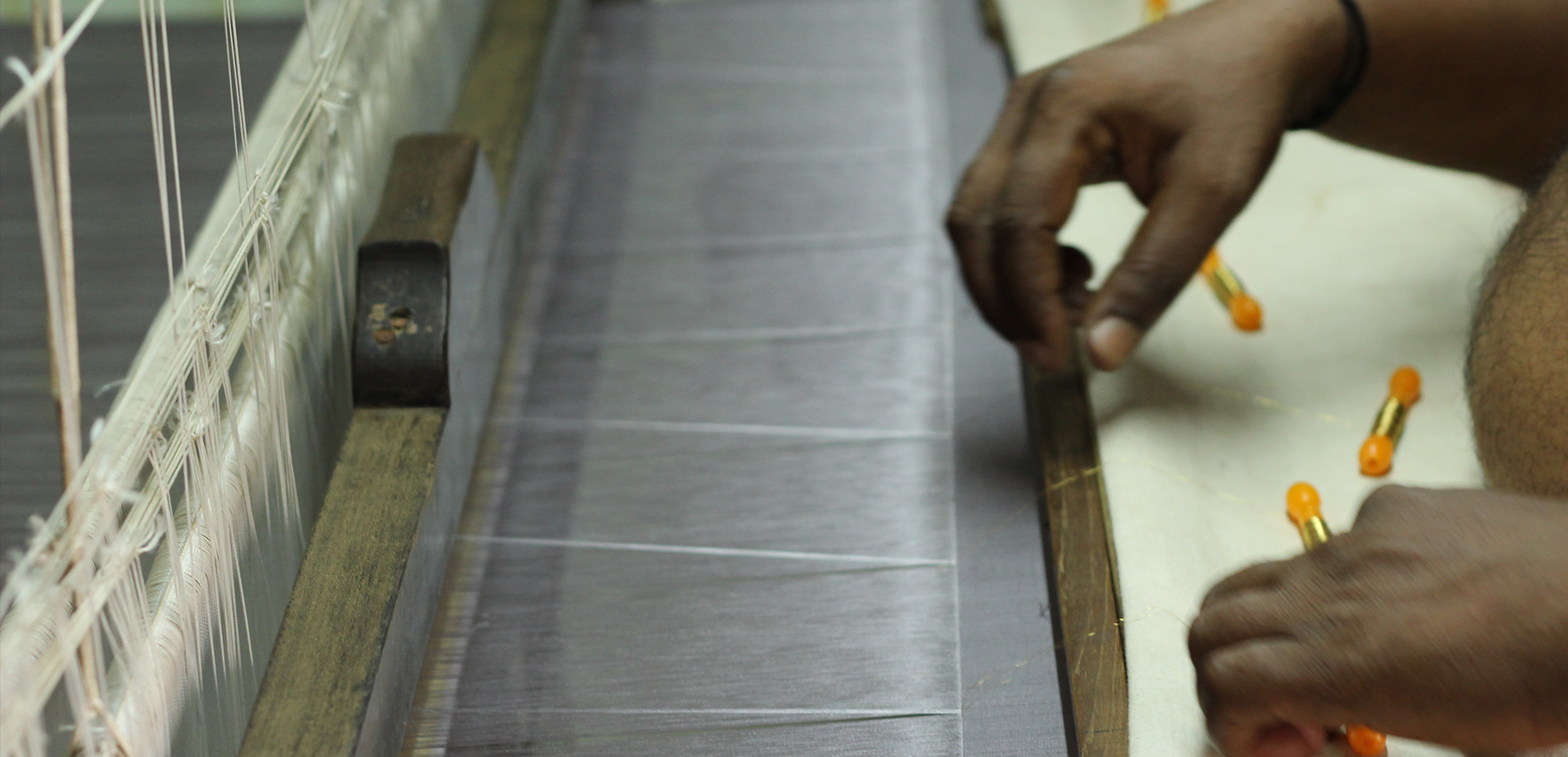
A Kanjivaram weaver setting up warp in his loom
Introduction
Kanchipuram Silk is a type of silk saree made in the Kanchipuram region in Tamil Nadu, India. The sarees are considered as the Southern Indian version of Banarasi saris. It has been recognized as a Geographical indication by the Government of India in 2005-06.
As of 2008, an estimated 5,000 families were involved in sari production. There are 25 silk and cotton yarn industries and 60 dyeing units in the region.
Mapping the System
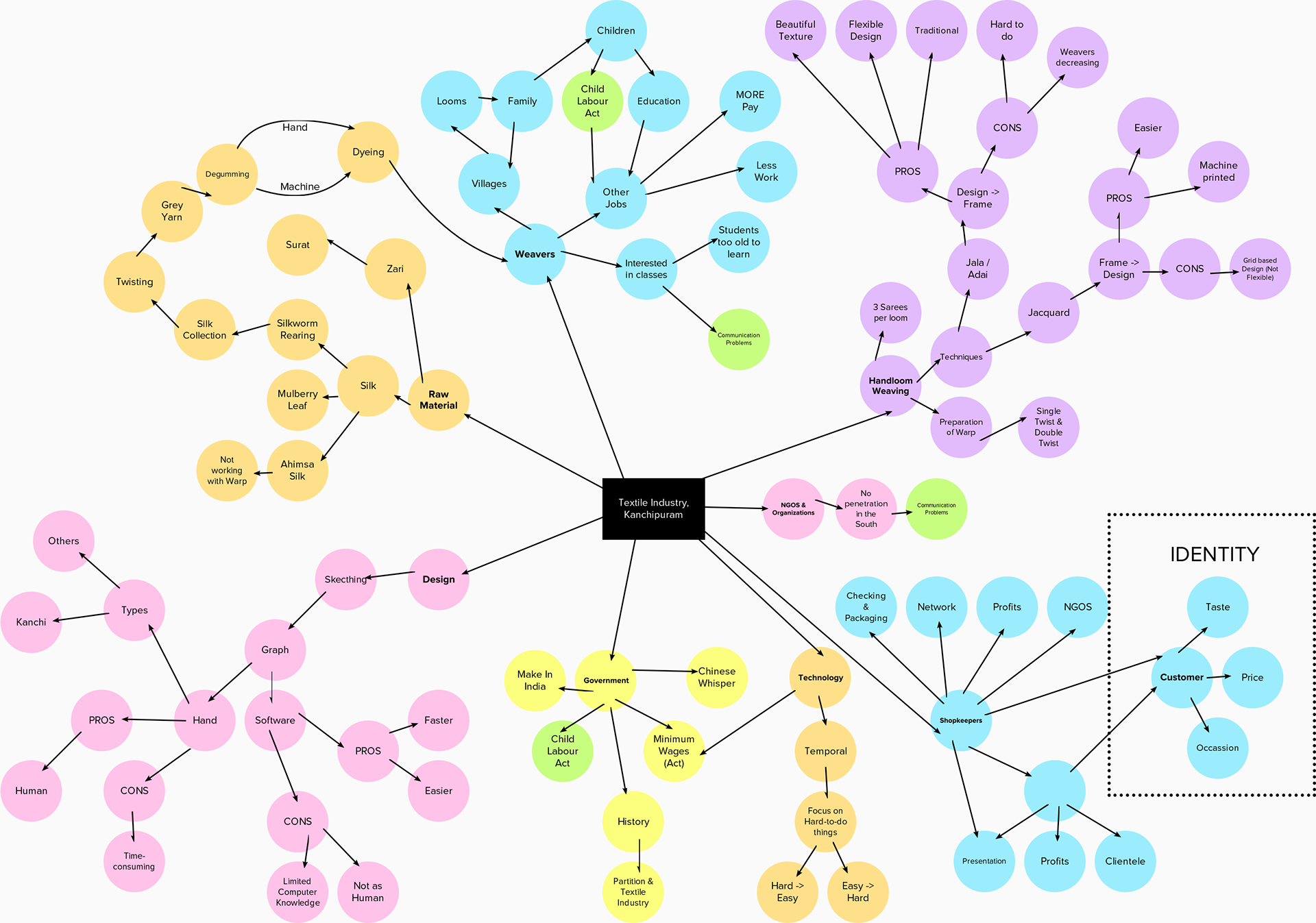
History
According to Hindu mythology, Kanchi silk weavers are the descendants of Sage Markanda, the master weaver of Gods who is supposed to have woven tissue from lotus fiber. Also, while cotton is considered to be the favourite fabric of Lord Shiva, silk was preferred by Lord Vishnu.
Raw Materials
The raw materials needed to make a Silk saree are the zari or gold thread and silk from the silk worm. The zari for Kanjivaram sarees are brought from Surat and the Silk from Ramanagara near Bangalore. The silk is mulberry silk, which means that the silkworm is fed mulberry leaves before the silk is harvested out of it.
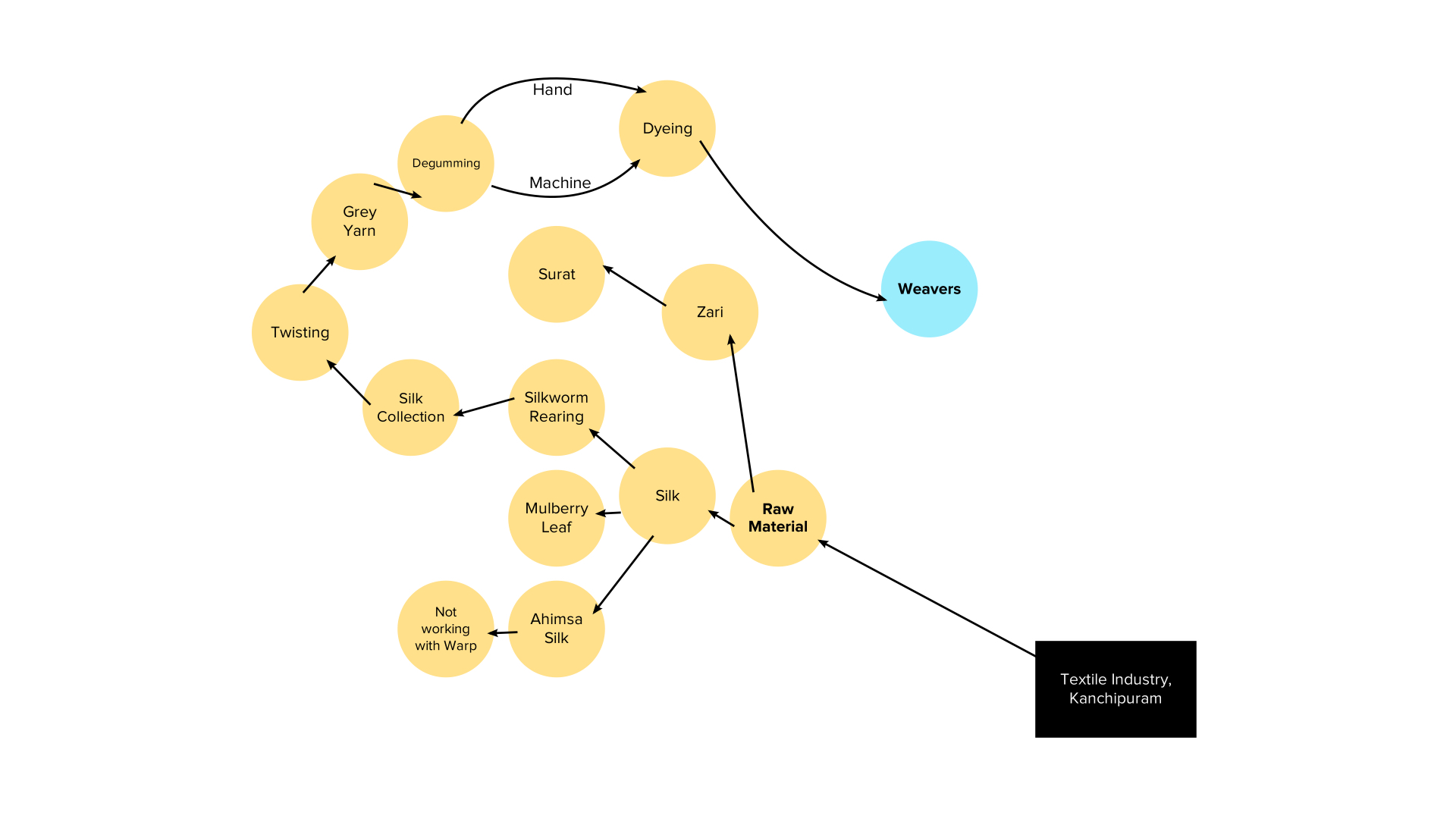
Grey Yarn from Ramanagara
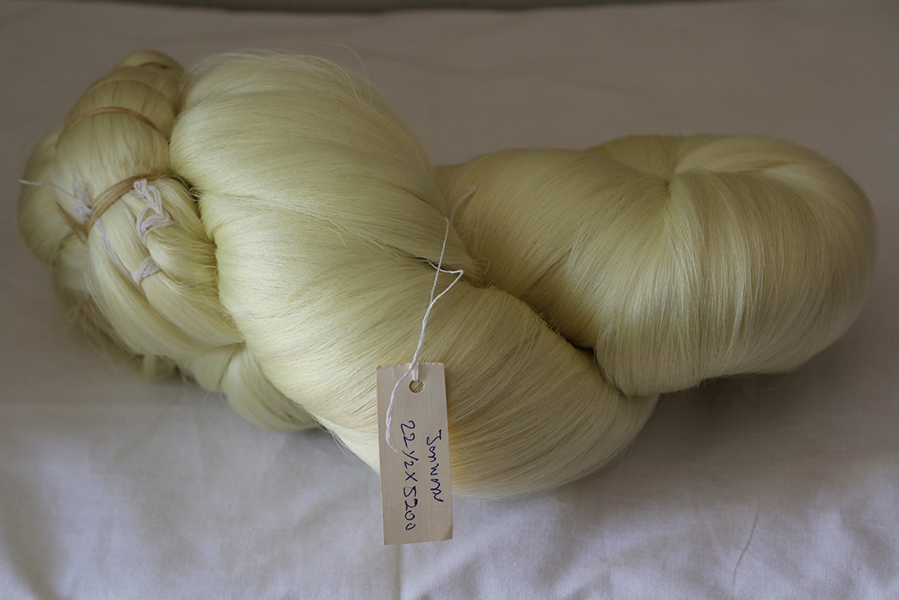
The grey yarn is degummed till it becomes white
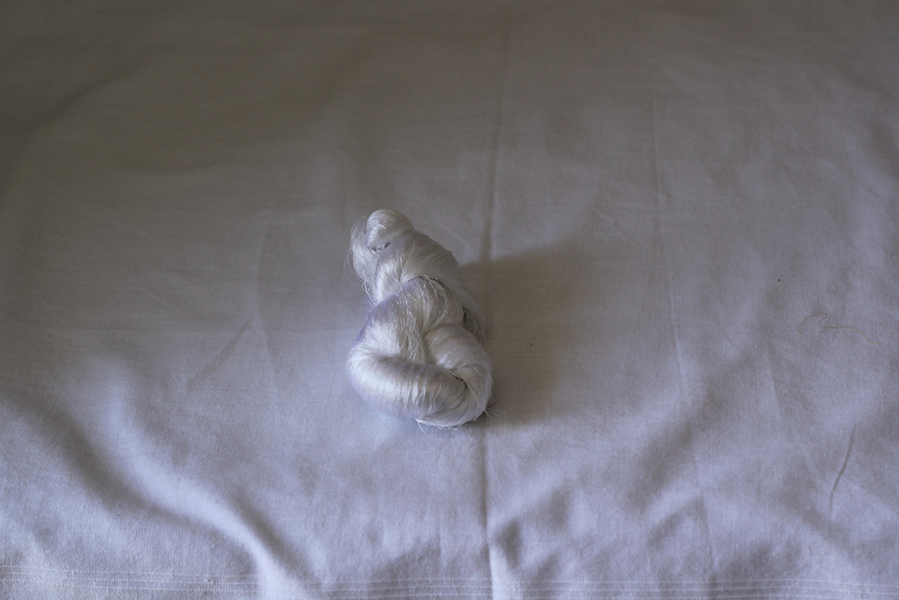
The dyed silk yarn
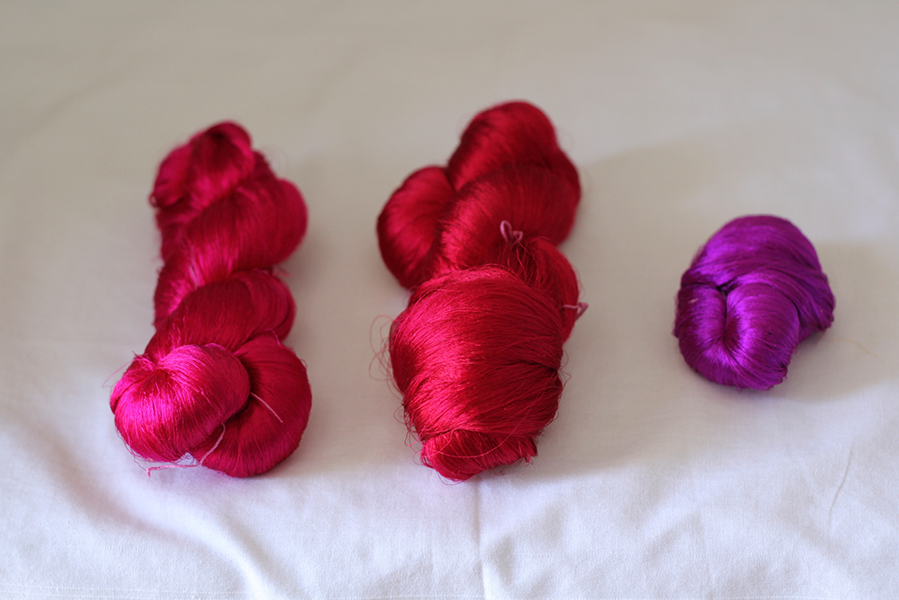
The zari thread from Surat
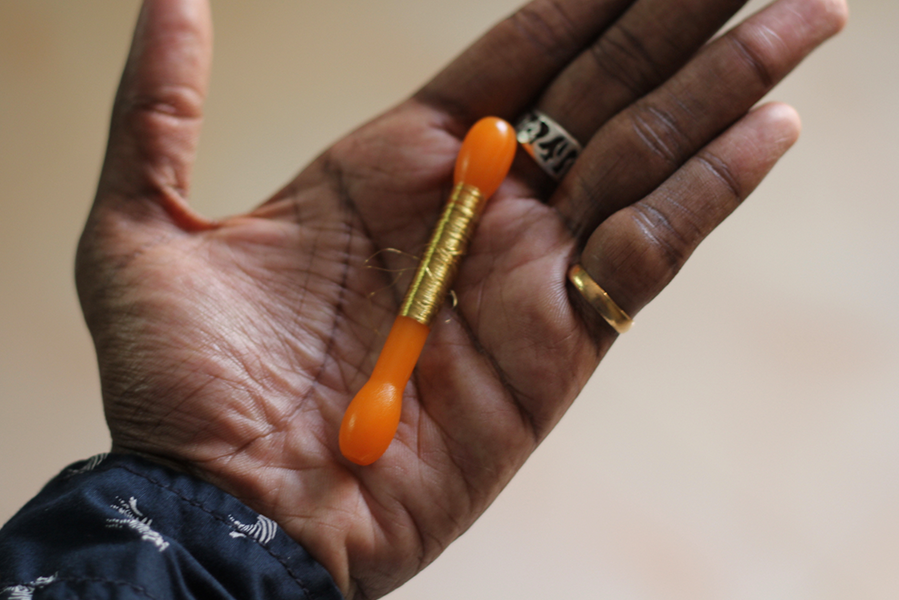
Design
Saris are distinguished by their wide contrast borders. Temple borders, checks, stripes and floral (buttas) are traditional designs found on a Kanchipuram sarees. The patterns and designs in the kanchipuram sarees were inspired with images and scriptures in South Indian temples or natural features like leaves, birds and animals. These are sarees with rich woven pallu showing paintings of Raja Ravi Varma and epics of Mahabharata and Ramayana. Kanchipuram sarees vary widely in cost depending upon the intricacy of work, colors, pattern, material used like zari (gold thread) etc. The silk is also known for its quality and craftsmanship, which has helped earn its name.
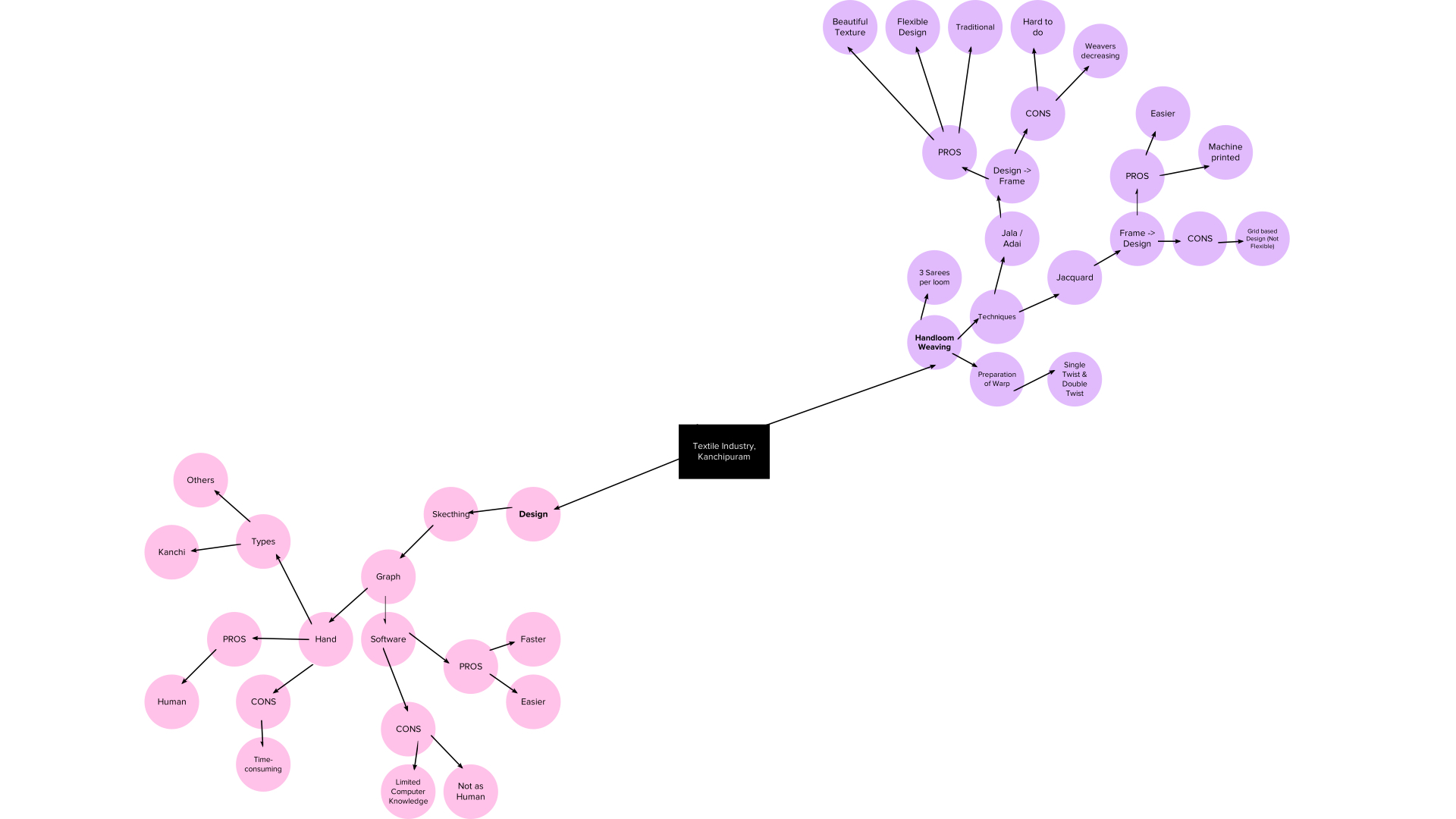
Sketches from a designer
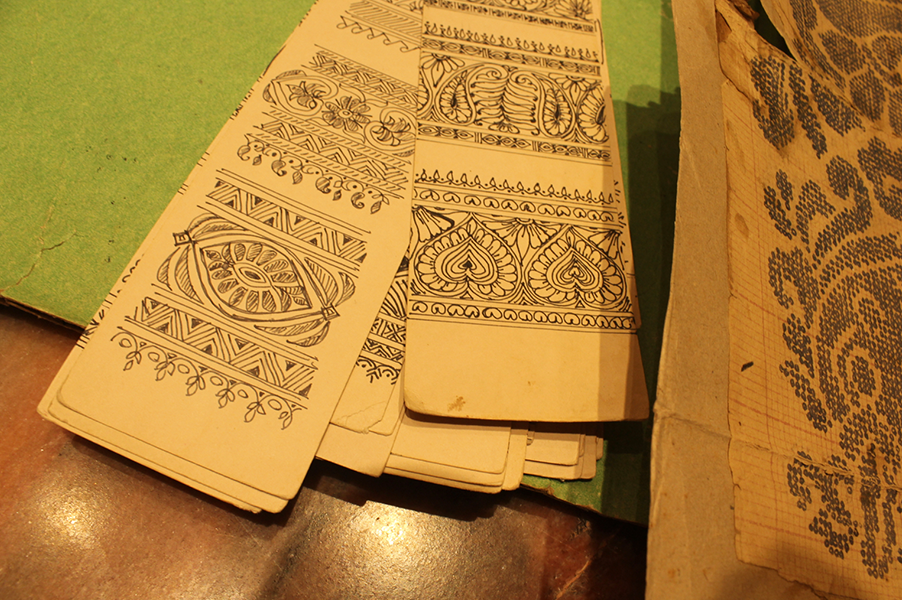
The sketches plotted on a graph
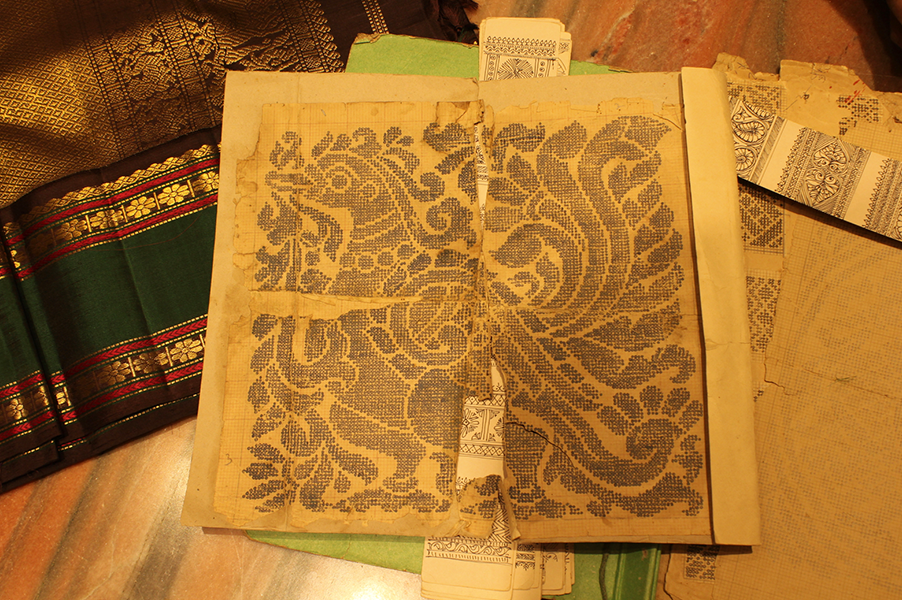
Weaving
The sarees are weaved from pure mulberry silk thread. The pure mulberry silk used in the making of Kanchipuram saris comes from South India and the zari comes from Gujarat. To weave a Kanchipuram sari three shuttles are used. While the weaver works on the right side, his aide works on the left side shuttle. The border color and design are usually quite different from the body. If the pallu (the hanging end of the sari) has to be woven in a different shade, it is first separately woven and then delicately joined to the Sari. The part where the body meets the pallu is often denoted by a zig zag line. In a genuine Kanchipuram Silk Sari, body and border are woven separately and then interlocked together. The joint is woven so strongly that even if the sarees tears, the border will not detach.That differentiates the kanchivaram silk sarees from the others.
Jacquard card
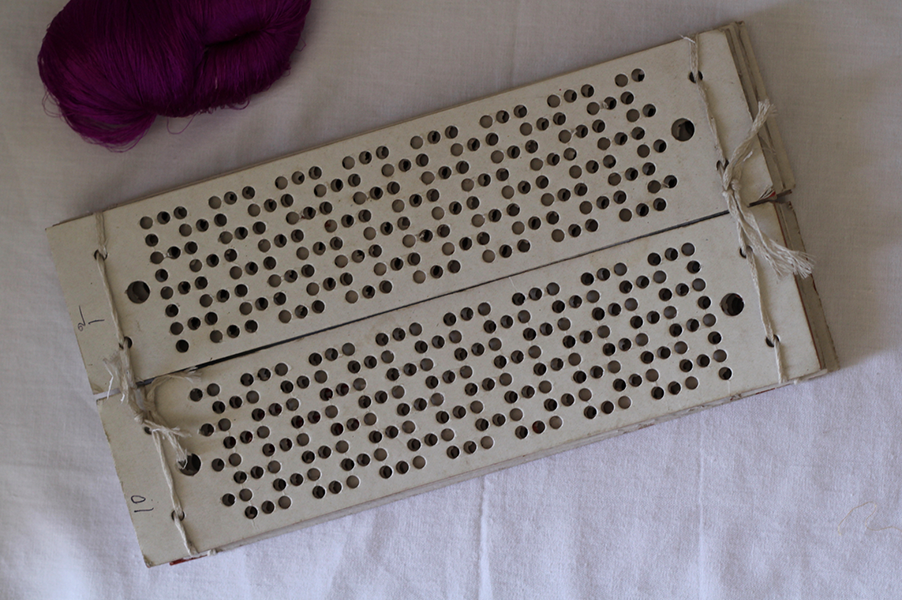
Jacquard mechanism on a loom
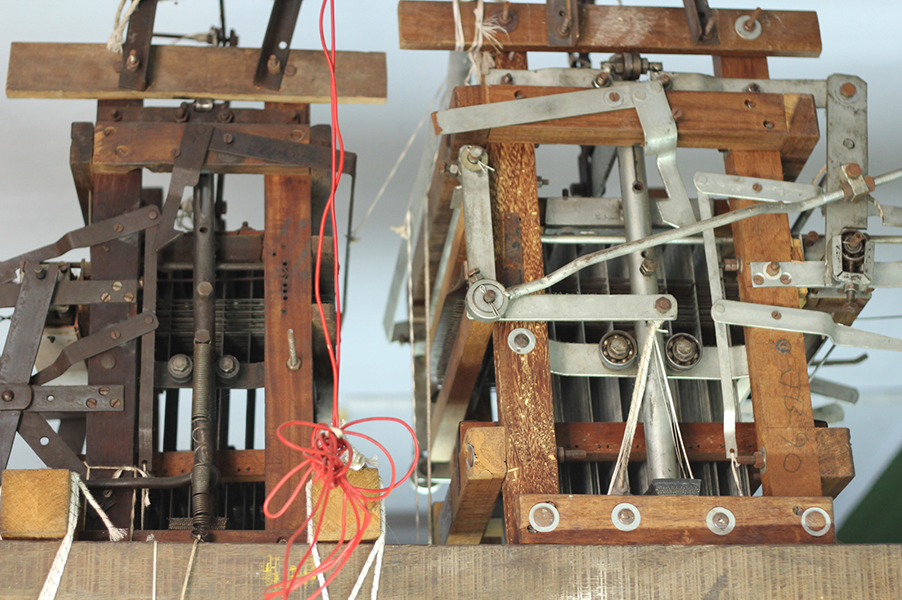
The second type of weaving in handlooms is called Jala or Adai as it is popularly known down south. The technique works like morse code with dots and dashes which come from the design.
Jala/Adai arrangement in a loom
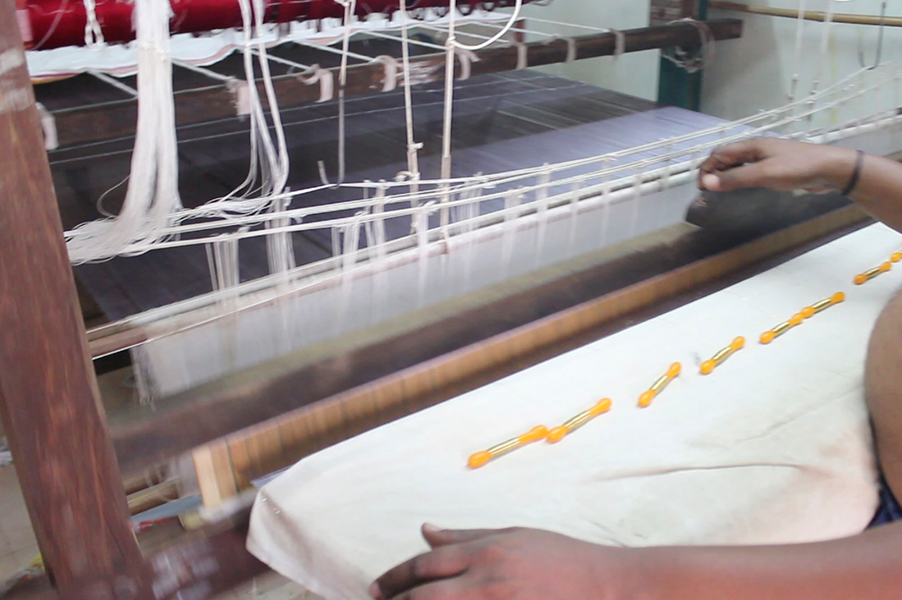
Saree with a Jala/Adai
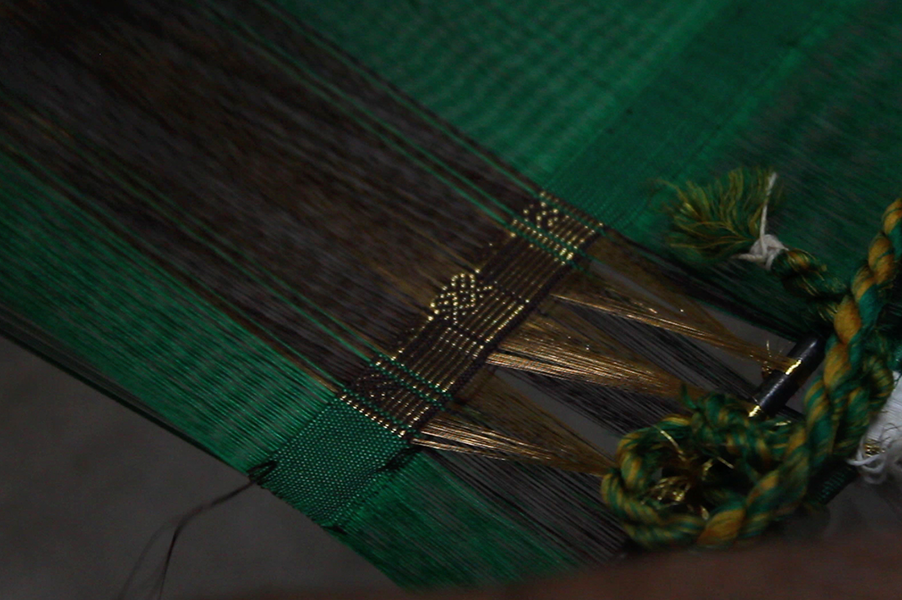
Weavers
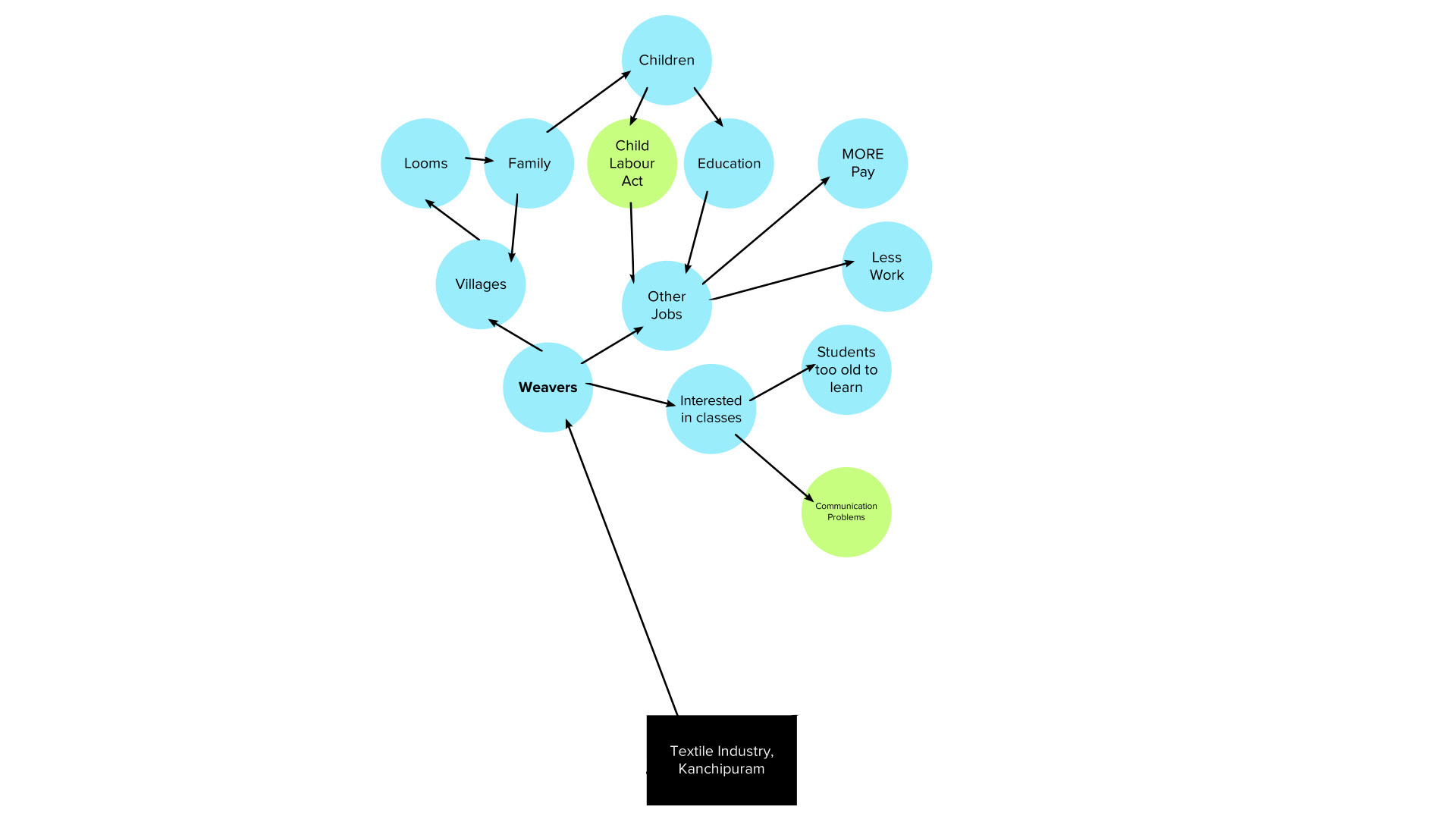
Weavers and the community are moving away from the profession to easier jobs that pay more, like ATM security guards, etc. They are not able to share their knowledge because of communication problems as well.
Government
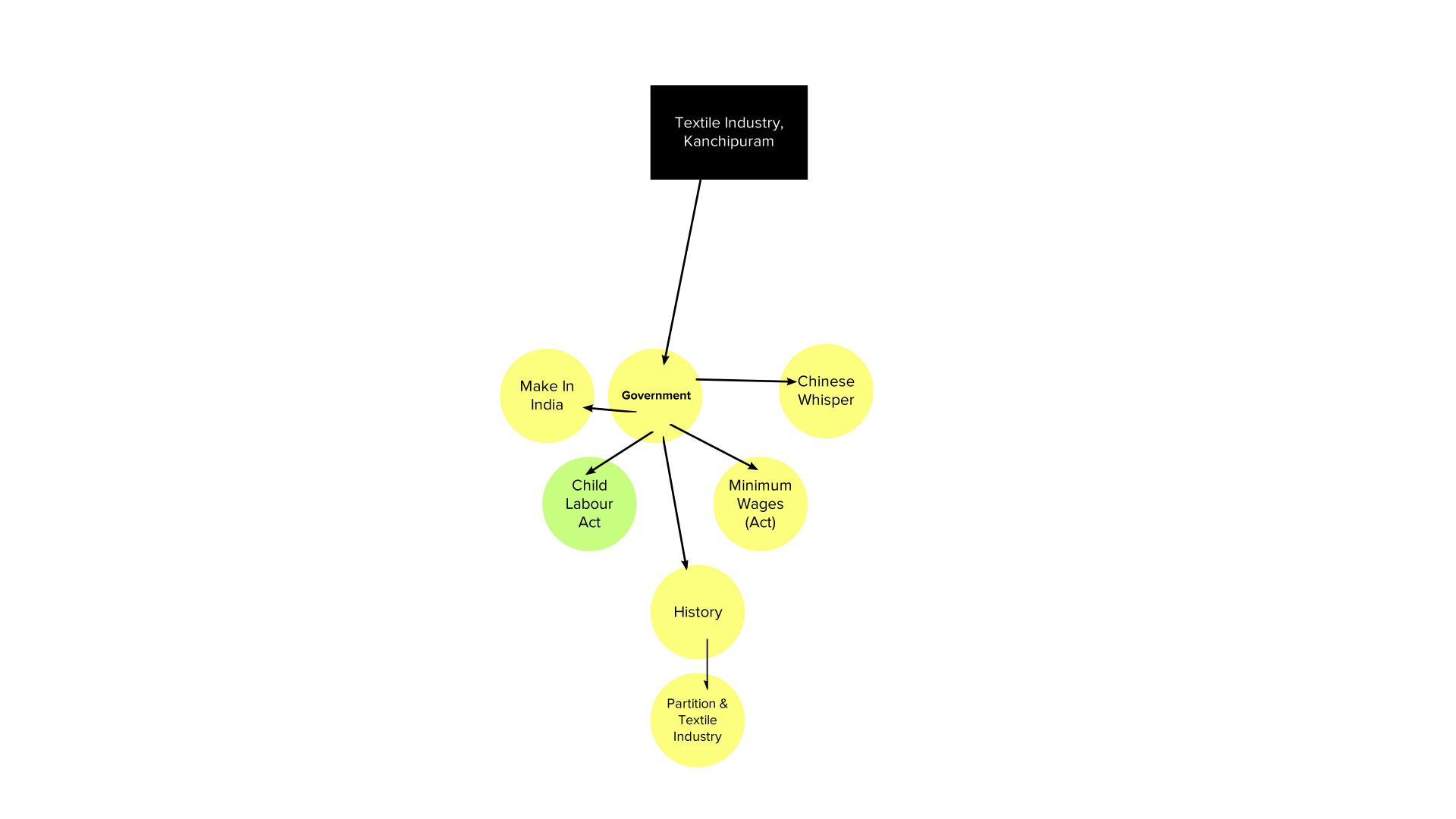
Technology
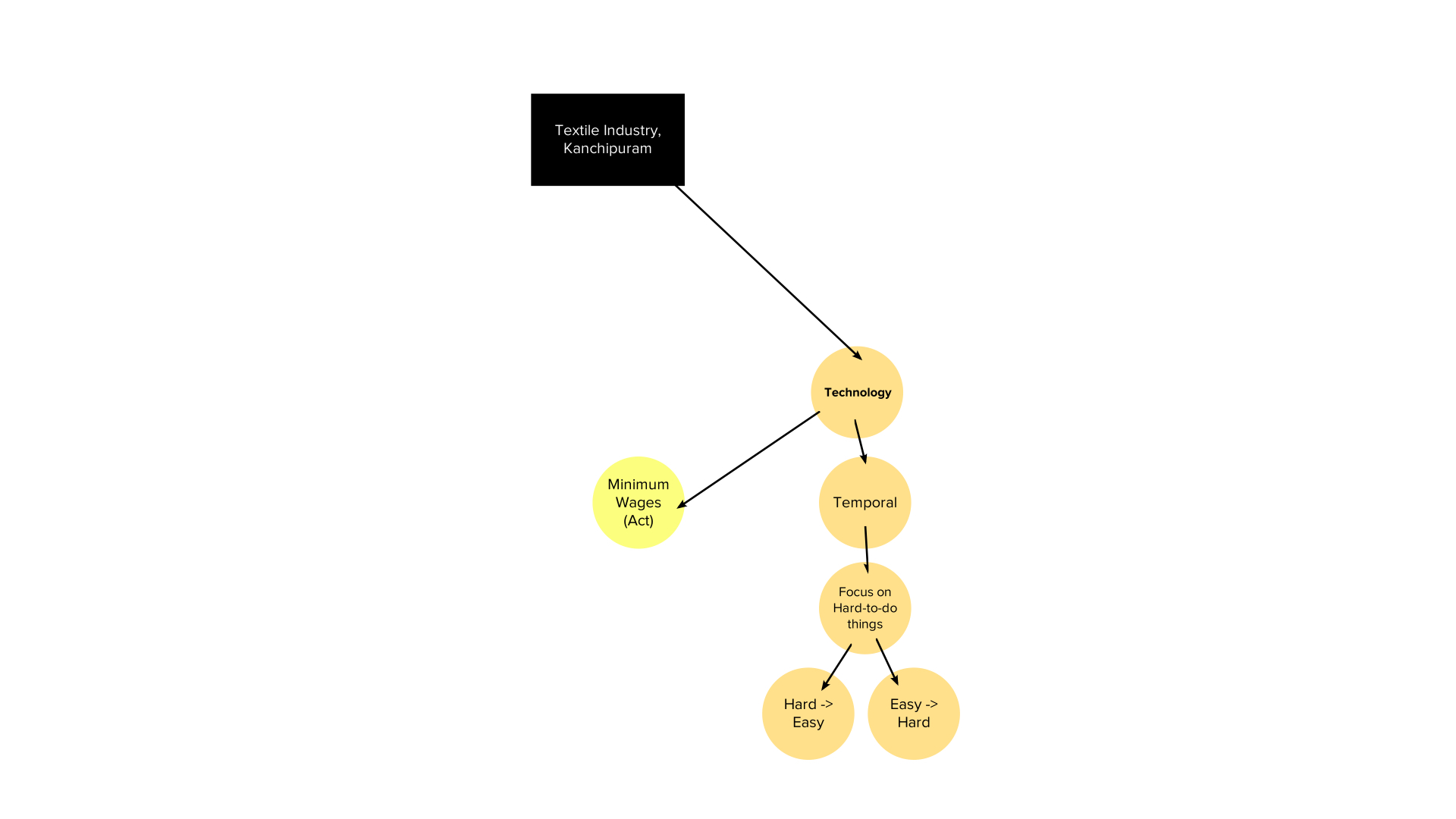
NGOs & Organizations
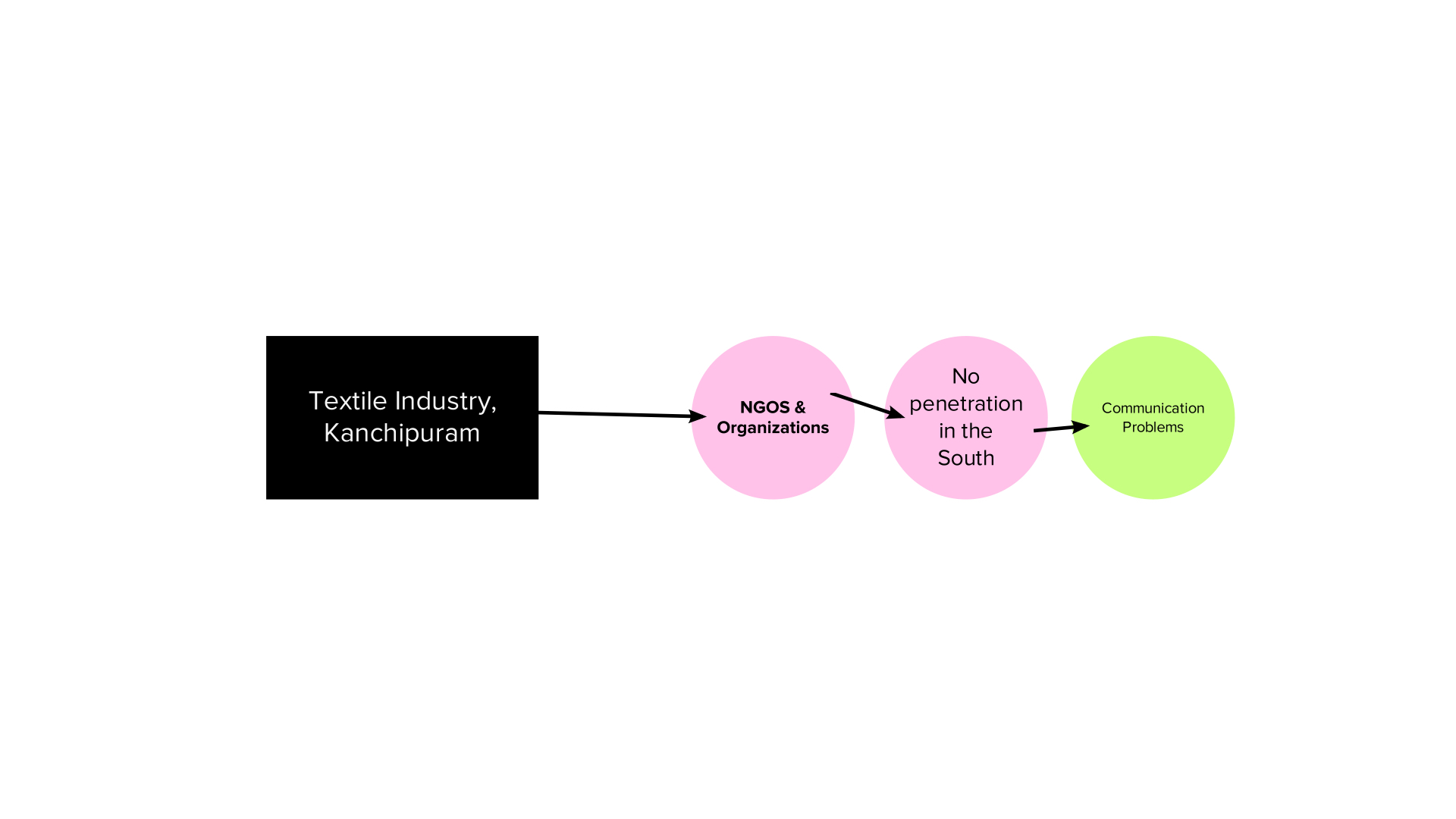
Consumers & Customers - The Identity Crisis
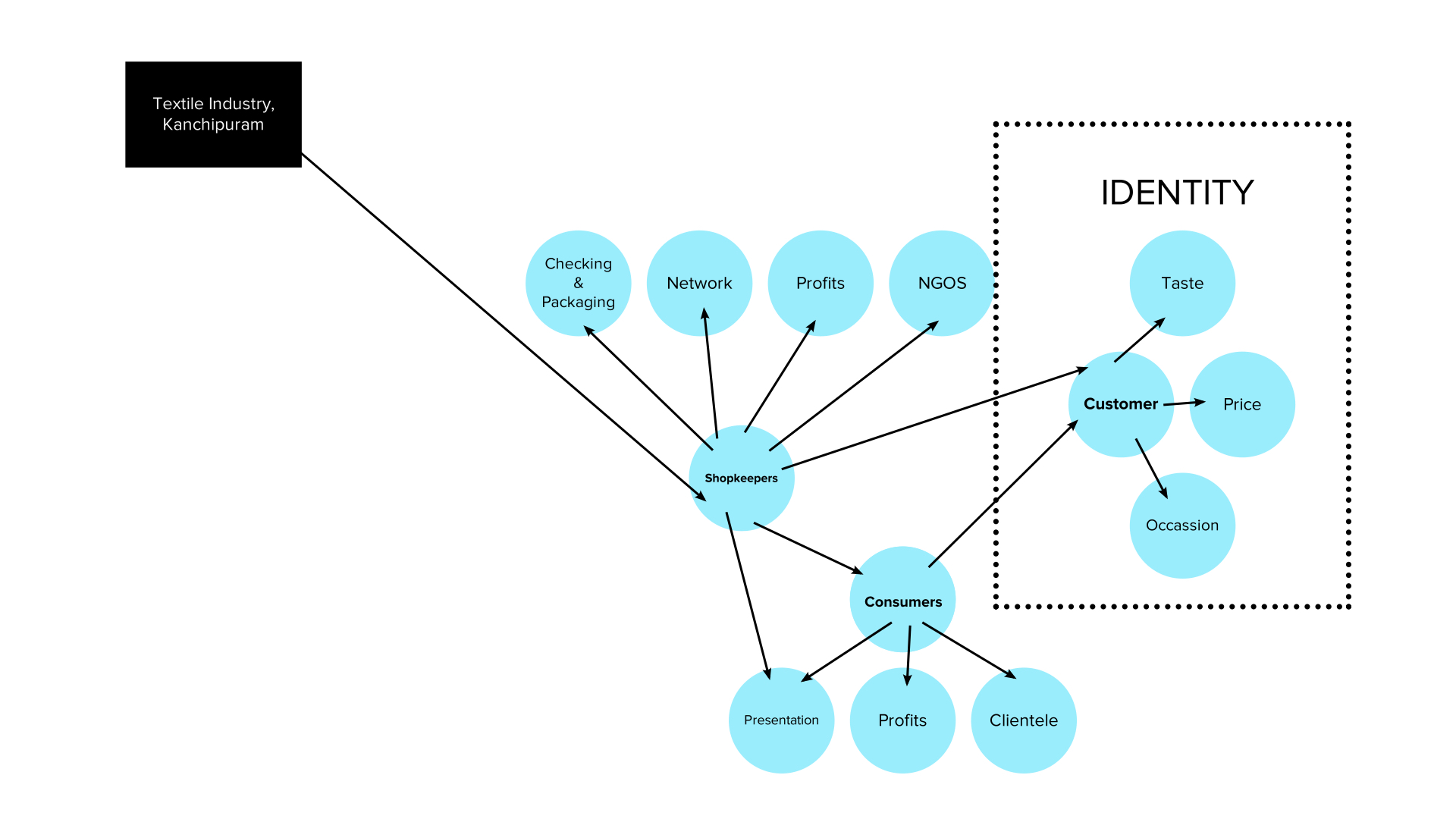
Significance
Kanchipuram saris woven with heavy silk and gold cloth are considered to be special and are worn on occasions and festivities.
Geographical Indication
In 2005, the Government of Tamil Nadu applied for Geographical Indication for Kanchipuram sarees. The Government of India recognized it as a Geographical indication officially since the year 2005-06.
Deliverable
The final deliverable with all the research that was done came to a website. The point of it was to bring the weavers and customers closer and bridge the gap. The initial version of the proposed website had its own teachings.
Usability Testing
The Direction
This was a very personal project. The learnings that came from it have helped shape me as an individual and changed the way I look at things.
I am currently working on making this project come to life, in a different direction.
Please connect with me if you are interested more in this.
Thank you for your time.